메르의 팜
삼성전자 근황 A/S(feat HBM3E,엔비디아, 펠리클, 한미반도체)
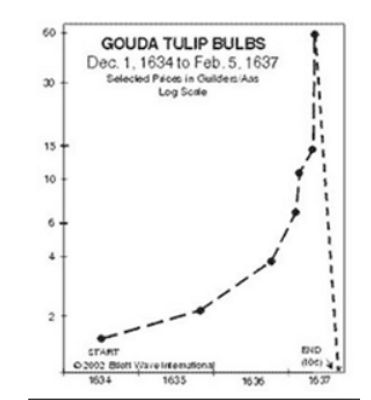
메르
2024.05.28
삼성전자관련 기사들이 계속 나오는듯해서, AS해봅니다.
삼성전자의 HBM 도전에 관한 글을 쓴적이 있다.
https://blog.naver.com/ranto28/223450673120
삼성전자, 엔비디아 HBM 공급 문제 근황(feat SK하이닉스, TSMC)
HBM과 관련해서 논란이 있어 정리해봅니다. https://www.newsworks.co.kr/news/articleView.html?idxno...
위 글의 한줄코멘트에서 다음과 같이 이야기 했다.
한 줄 코멘트. SK하이닉스가 권투선수고, TSMC가 레슬링 선수, 애플이 유도선수라면 삼성전자는 종합격투기 선수다. 삼성전자가 힘든 점은 SK하이닉스와는 권투, TSMC와는 레슬링, 애플과는 유도시합을 해야 하는 상황이다.
삼성전자가 쉽지않은 싸움을 하고있다는 말이다.
삼성전자가 수장을 바꿨다.
경계현 사장을 미래사업기획단의 단장이었던 전영현 부회장과 교체한 것이다.
https://www.yna.co.kr/view/AKR20240521035651003?input=1195m
[2보] 삼성전자, 반도체 수장 전격 교체…새 수장에 전영현 부회장 | 연합뉴스
(서울=연합뉴스) 장하나 기자 = 삼성전자[005930]가 반도체 사업의 새 수장으로 전영현(64) 미래사업기획단장(부회장)을 임명했다.
삼성의 미래사업기획단은 작년연말 정기인사때 만들어진 신설조직이다.
임원급을 보면, 단장을 전영현 부회장으로 하고, 정성택 부사장과 이원용 상무가 단원이 되었다.
정성택 부사장은 1976년생으로 미국 스탠퍼드 석박사이후 퀄컴에 근무했고, 매캔지와 골드만삭스등에 근무한 이력이 있다.
정성택 부사장은 지금까지 삼성전자의 미래 먹거리 발굴을 주력하는 신사업 TF팀장을 맡고 있었다.
인수합병(M&A)전문가다.
이원용상무는 MIT에서 석박사를 받은 인물로 BCG(보스턴컨설팅그룹)을 거쳐서 SAIT(삼성종합기술원)의 기획팀장으로 있었다.
미래산업기획단은 기술을 아는 M&A인력들로 조직을 갖춘 모양새라, 퇴직자들을 모아놓는 한직은 아닌듯하다.
단장인 전영현부회장은 권오현 삼성전자 전회장과 함께 삼성전자 메모리 반도체를 성장시킨 주역이다.
전영현부회장과 경계현 사장은 업무스타일이 극과 극이다.
경계현 사장이 부드럽게 직원들을 관리한다면, 전영현부회장은 직원들을 갈아넣어 성과를 내는 강한 리더쉽을 가지고 있다.
파운드리는 천재의 창의력으로 성과가 나오기보다, 연구진의 시간과 인력을 갈아넣어서 성과를 내는 영역이라는 평가다.
배합비율과 공정들을 끊임없이 미세하게 바꿔 최적 조합을 찾아나가며,야근 및 노가다로 수율을 올리는 경우가 많아서 그렇다.
TSMC대비 적은 연구인력과 테스트 설비로 그 이상의 성과를 내기위해서 인력을 강하게 운용해야 하겠다는 판단이 선듯하다.
로이터 통신에서 삼성전자가 엔비디아에 HBM3E를 납품하는 퀄 테스트에 Fail이 났다는 기사가 나왔다.
발열과 전력소비등을 잡지 못한것이 원인이라는 내용이다.
https://www.yna.co.kr/view/AKR20240524021451009?input=1195m
[2보] 로이터 "삼성전자 HBM칩 아직 엔비디아 테스트 통과 못해" | 연합뉴스
(서울=연합뉴스) 차병섭 기자 = 삼성전자가 미국 반도체업체 엔비디아에 고대역폭 메모리(HBM)를 납품하기 위한 테스트를 아직 통과하지 못했다고...
삼성전자는 즉시 반박하는 보도자료를 뿌렸다.
삼성전자는 24일 고대역폭 메모리(HBM)와 관련, “다양한 글로벌 파트너들과 HBM 공급을 위한 테스트를 순조롭게 진행 중”이라고 밝혔다.
삼성전자는 이날 공식 입장을 내고 “현재 다수의 업체와 긴밀하게 협력하며 지속적으로 기술과 성능을 테스트하고 있다”며 “HBM의 품질과 성능을 철저하게 검증하기 위해 다양한 테스트를 수행하고 있다”고 설명했다.
이어 “삼성전자는 모든 제품에 대해 지속적인 품질 개선과 신뢰성 강화를 위해 노력하고 있으며, 이를 통해 고객들에게 최상의 솔루션을 제공할 예정”이라고 덧붙였다.
https://www.mk.co.kr/news/business/11023591
[속보] 삼성전자, 외신보도 즉각 반박…“엔비디아 HBM 공급 테스트 순조롭게 진행 중” - 매일경제
로이터통신과 삼전 보도자료를 조합하면, 삼성전자 HBM3E가 테스트를 통과하지 못하고 있는것은 삼성전자가 확인해준셈이다.
통과는 못하고 있지만, 아직 Fail이 확정된 것이 아니고, 보완을 하고 있다는 내용으로 읽힌다.
경계현 사장을 교체한 이유가 이것때문이라고 봐야할듯하다.
삼성전자는 파운드리 수율을 잡아야 하는 숙제를 기본적으로 가지고 있다.
삼성전자가 수율을 잡지 못하는 이유로 펠리클에서 TSMC와 근본적인 차이가 있는 것으로 보는 전문가들이 있다.
펠리클은 일종의 먼지덮개다.
EUV 펠리클 / 미쓰이화학
EUV용 펠리클은 반도체 회로패턴을 그린 유리기판인 포토마스크에 먼지가 붙지 않도록 씌우는 얇은 필름이다.
펠리클은 얇은 정도가 극악하다.
서울시청 광장에 랩을 까는 상황으로 이해하면 된다.
삼성전자는 3나노 EUV공정을 펠리클 없이 생산을 하고 있다.
아무리 삼성이 먼지관리를 잘한다고 하더라도, 이것때문에 수율에 차이가 나는게 아닌가 하는 의구심이 있는 상황이다.
펠리클은 ASML이 캐나다 테라다인과 일본 미쓰이화학과 함께 만들고 있다.
펠리클은 투과율이 중요하다.
핸드폰을 예로들면 보호필름을 씌우더라도 화면이 깨끗하게 잘 보여야 하는 것과 비슷하다.
펠리클 역할(사진=메리츠증권)
3나노를 양산하기 위해서는 최소 투과율 90%가 필요하다.
기존 노광기는 빛이 위에서 내려와 패턴을 그렸지만, EUV장비는 빛이 거울에 반사돼 웨이퍼에 닿는 구조라, 빛의 손실이 훨씬 크다.
빛의 손실이 큰데, 펠리클을 통과하는 과정에서 빛의 추가손실이 많으면 패턴이 잘 그려지지 않는다.
3나노의 경우 90%이상 투과율에 50나노급 이하 두께의 얇은 펠리클이 필요하고, EUV의 강한 빛이 펠리클을 통과하면서 발생하는
열에 손상이 가지않는 내구성이 요구된다.
1만시간 정도 사용할 수 있는 펠리클 한장에 3만5천달러까지 하는 비싼 소모품이지만, 수율을 올릴수 있다면 밥값은 하는 것이다.
ASML은 투과율 90%의 MK 4.0을 개발했고, 미쓰이화학이 시제품을 생산하고 있지만, 아직 양산을 못하고 있다.
삼성전자는 펠리클을 만드는 한국 기업 2곳에 각각 658억과 430억을 투자해 90%이상 투과율이 나오는 펠리클 개발을 진행하고 있고, ASML의 4.0 양산을 기다리고 있다.
개발속도가 빠른 ASML의 4.0을 우선적으로 사용하되, 한국기업이 개발 및 양산에 성공하면 교체를 염두에 두고있는듯하다.
TSMC는 자체제작한 펠리클을 사용하고 있다.
이런점이 파운드리에 집중해온 TSMC의 저력이기도 하다.
펠리클이 장점만 있는것이 아니다.
펠리클을 쓰면 수율은 올라가지만 생산량이 떨어질 가능성이 높아진다.
워낙 얇아서 펠리클은 잘 깨진다.
한번 펠리클이 깨지면 이것을 교체하기 위해 EUV를 며칠씩 세워야 한다.
삼성전자에 몇십대 없는 EUV중 1대가 며칠씩 가동을 중단하는 것은 생산량에 영향을 꽤 미치는 일이다.
ASML의 펠리클은 시제품 단계라 공급량도 충분하지 않다.
미쓰이화학에서 ASML의 펠리클을 만들고 있는데, 수율이 30%가 안나오는 것으로 알려지고 있다.
10개 만들면 7개가 불량이라는 말이고, 펠리클을 도입한다고 결정해도 수율을 잡기전까지는 충분한 공급이 힘들수 있다.
투과도를 높이려면 앏게 만들어야 하고, 앏게 만들면 잘깨지는 애매한 상황이다.
TSMC가 2019년부터 자체적으로 만들어 사용하고 있는 펠리클은 투과율 85%선으로 알려지고 있다.
사진=TSMC
TSMC가 온전한 성능을 보여주는 3나노가 아니라, 한두가지씩 하자가 있는 3나노를 만드는 이유가, 자체제작 펠라클의 투과율이 약한 것이 원인이라는 분석이 나오는 이유다.
펠리클 없이 3나노를 뽑아내고 있는 삼성전자에 90% 펠리클이 부착될때 수율과 생산량이 어떻게 될지 관전포인트가 될 듯하다.
HBM3E는 한미반도체가 관건이 될지 모른다.
삼성전자는 10여년전 한미반도체가 소송을 제기하면서 한미반도체와 거래를 끊은 상태다.
삼성전자의 계열사로 1993년에 설립한 세크론이라는 반도체 장비기업이 있다.
한미반도체는 반도체칩을 제품화하는 삼성전자의 패키징 공정에 소잉 앤드 플레이스먼트 장비를 납품했다.
2000년대 초반 한미반도체가 자체 개발한 장비로, 반도체 패키지 절단, 세정, 건조, 검사, 선별 및 적재 공정을 하나의 장비에서 가능하도록 해 시장에서 호응을 얻었다.
한미반도체는 “제품 개발 후 삼성전자에 제품을 공급했지만, 세크론이 대체 장비를 공급하기 시작하면서 납품이 중단됐다”며
연구개발로 확보한 기술을 세크론이 무단으로 사용해 장비를 제조하고 삼성전자등에 납품했다고 소송을 제기했다.
협력업체에게 소송을 당한 경험이 없었던 삼성전자는 당황하고 분노했다.
한미반도체는 소송에서 이겼고, 삼성전자는 소송을 제기한 한미반도체와 거래를 끊었다.
https://www.etnews.com/201209060516
한미반도체, 삼성전자 자회사 세크론과 특허 소송서 승소
한미반도체는 메모리반도체에 활용되는 TC본더 부문에서 세계 선두 업체로 꼽힌다.
TC본더는 칩과 칩을 쌓을 때 정렬이 틀어지지 않도록 하는 단계에서 활용되는 장비다.
일정 시간 동안 열과 압력을 가해 층층이 쌓인 칩이 안정적으로 자리 잡도록 돕는다.
HBM은 D램 여러 개를 수직으로 올린 다음 1024개의 구멍을 통해 연결하기 때문에, D램을 정확하게 위치시키는 작업이 필요하다.
단수가 8단에서 12단으로 높아질수록 공정에 투입하는 TC본더의 숫자도 많아진다.
한미반도체의 TC본더는 삼성전자와 마이크론이 채택한 열압착(TC) 필름(NCF)에도 활용할 수 있다.
삼성전자가 한미반도체의 TC본더를 도입하는 데 있어 공정상의 문제점은 없는 셈이다.
현재 삼성전자가 TC본더를 구매해 온 업체는 세메스(구 세크론),일본 토레이와 신카와등이다.
삼성전자는 자회사인 세메스를 패스하고 외부업체인 한미반도체에 본딩 장비를 받는것이 부담스러울수 있다.
하지만, 세메스는 열로 압착하는 TC본더가 아니라 칩(다이)을 프레임에 접착하는 다이본더(Die Bonder)를 주로 만들던 곳이다.
TC본더는 HBM 5세대인 HBM3E까지만 사용이 가능한것으로 평가되고 있다.
6세대부터는 하이브리드본딩이라는 새로운 기술이 사용된다.
세메스나 한미반도체 모두 하이브리드본딩에 도전하고 있다.
TC본더는 한미반도체를 사용하고, 세메스가 하이브리드본딩에 성공하면 차세대에서 세메스를 활용하는 방법도 가능할듯하다.
한미반도체가 SK하이닉스에 TC본더를 납품하며, SK하이닉스의 안정적인 수율과 성능에 일조를 한만큼, 삼성전자가 한미반도체의 TC본더를 사용한다면 HBM3E에 도움이 될 가능성이 있어보인다.
삼성전자의 바뀐 수장이 과거 감정을 버리고 한미반도체와 손을 잡을지도 관전포인트중 하나일듯하다.
발열은 조금 다른 문제다.
HBM은 열을 많이 발생시키기때문에 열을 잡는것이 중요하다.
SK하이닉스는 HBM 칩 전체에 납땜을 하고, 칩 사이에 액체 보호재를 넣어서 공백을 채우는 방식을 사용해서 발열을 잡고있다.
MR-MUF라는 방식이다.
아무래도 액체가 칩사이에 있다보니 발열을 잡기 유리하다.
삼성전자와 마이크론은 칩 사이에 필름을 층층이 까는 방식으로 발열을 잡고 있다.
TC NCF라는 방식이다.
칩사이에 액체가 있는 방식보다는 필름을 까는형식이 아무래도 발열을 잡는데 불리하다.
다만, 마이크론과 경쟁한다는 입장으로 보면, 삼성전자와 마이크론은 같은 NCF방식을 사용하고 있다.
삼성전자가 마이크론보다 조금 더 업그레이드된 자체기술을 NCF에 적용시키고 있어서 마이크론과 경쟁은 해볼만한듯하다.
NCF로 MR-MUF의 발열수준을 따라가려면 필름을 훨씬 얇게 만들어 여러장 깔아야한다.
삼성전자는 층수가 많아지면 휘어짐 문제가 있는 MR-MUF보다 NCF가 유리할 것이라는 주장이고, SK하이닉스는 16단까지 MR-MUF방식으로 양산을 할 것이라고 주장이 나누어지고 있다.
양측의 주장이 엇갈리는 또 하나의 관전포인트로 보인다.
한줄 코멘트. 엔비디아에 HBM3E를 공급하는 업체로 SK하이닉스는 확정이고, 나머지 한자리를 가지고 마이크론과 삼성전자가 경쟁을 하는 형국이다. 마이크론은 아직 수율이 20%에도 미치지 못하는 단계로 알려지고 있어, 삼성전자가 기회를 완전히 놓친것은 아닌듯하다. 삼전의 주주는 아니지만, 한국경제를 위해 좋은 소식이 들렸으면 좋겠다.
댓글 1
- Jackie Chan · 일 년 전삼전은 기필코 일어서리